FAQ
What Materials are Available for Spot Welding Electrodes?
In the production of resistance welding, welding parts of different materials and shapes need to be equipped with electrodes of different materials and shapes. The influence of electrodes on the welding quality during continuous welding exceeds more than 50%. Choose suitable welding materials and electrode pairs for welding. Quality is important!
1. Chromium Zirconium Copper (CuCrZr)
Chromium-zirconium copper (CuCrZr) is the most commonly used resistance welding electrode material, which is determined by its excellent chemical and physical properties and good cost performance.
1. The chromium-zirconium-copper electrode achieves a good balance of the four performance indicators of the welding electrode:
Excellent electrical conductivity-to ensure that the impedance of the welding circuit is minimized, and excellent welding quality is obtained
High-temperature mechanical properties-higher softening temperature to ensure the performance and life of electrode materials in high-temperature welding environments
Abrasion resistance-the electrode is not easy to wear, prolong the life and reduce the cost
Higher hardness and strength-to ensure that the electrode tip is not easily deformed and crushed under a certain pressure, and the welding quality is guaranteed
2. The electrode is a consumable for industrial production, and the amount is relatively large, so its price and cost are also an important factor to consider. For the relatively good performance of the chromium zirconium copper electrode, the price is relatively cheap and can meet the needs of production.
3. The chromium zirconium copper electrode is suitable for spot welding and projection welding of carbon steel plates, stainless steel plates, plated plates and other parts. The chromium zirconium copper material is suitable for manufacturing electrode caps, electrode connecting rods, electrode heads, electrode holders, and projection welding special electrodes , Welding wheels, contact tips and other electrode parts.
The standard electrode heads, electrode caps, and heterogeneous electrodes produced adopt cold extrusion technology and precision machining to further increase the density of the product, the product performance is more excellent, durable, and the welding quality is stable.
2. Beryllium copper (BeCu)
Compared with chromium zirconium copper, beryllium copper (BeCu) electrode material has higher hardness (up to HRB95~104), strength (up to 600~700Mpa/N/mm²) and softening temperature (up to 650℃), but its conductivity It’s much lower and worse.
The beryllium copper (BeCu) electrode material is suitable for welding plate parts with greater pressure, and harder materials, such as seam welding wheels; it is also used for electrode accessories with higher strength requirements such as crank electrode connecting rods. A converter for robots; at the same time, it has good elasticity and thermal conductivity, which is very suitable for manufacturing nut welding chucks.
The cost of beryllium copper (BeCu) electrode is relatively high, and we usually list it as a special electrode material.
3. Alumina copper (CuAl? O?)
Alumina copper (CuAl? O?) is also called dispersion strengthened copper. Compared with chromium zirconium copper, it has excellent high temperature mechanical properties (softening temperature up to 900°C) and higher strength (up to 460~580Mpa/N/mm²) , And good electrical conductivity (80~85IACS%), excellent wear resistance and long life.
Alumina copper (CuAl? O?) is a kind of electrode material with excellent performance, regardless of its strength, softening temperature and good electrical conductivity, it is especially prominent for welding galvanized plates (electrolytic plates), it does not look like The chromium-zirconium-copper electrode has the phenomenon that the electrode sticks to the workpiece, so there is no need for frequent grinding, which effectively solves the problem of welding galvanized sheets, improves efficiency and reduces production costs.
Alumina copper electrode has excellent welding performance, but its current cost is very expensive, so it cannot be widely used at present. As the current galvanized sheet is widely used, the excellent welding performance of aluminum oxide copper on the galvanized sheet makes its market prospect extremely broad.
Alumina copper electrode is suitable for welding parts such as galvanized sheet, hot formed steel, high-strength steel, aluminum products, high-carbon steel plate, stainless steel plate and so on.
4. Tungsten (W), Molybdenum (Mo)
Tungsten electrode materials include pure tungsten, tungsten-based high-density alloys and tungsten-copper alloys. Tungsten-based high-density alloys are sintered by adding a small amount of nickel-iron or nickel-copper to tungsten. Tungsten-Copper ) Containing 10-40% (weight ratio) of copper.
Molybdenum tungsten and molybdenum electrodes have the characteristics of high hardness, high burning point, and excellent high temperature work performance. They are suitable for welding non-ferrous metals such as copper, aluminum, nickel, etc., such as the welding of copper braid and metal sheets of switches, and silver dots. Brazing, etc.
Send Message
Premium Product
Catalogue
News & Technicals
Structure of Nut Electrode of Intermediate Frequency Spot Welder
Analyze the Electrode of the Intermediate Frequency Spot Welder
Analyze the Influence of the Welding Point Distance of the Spot Welder
Function of Butt Welding Machine Inspection System
Contact Us
Email: info@resistancewelder.com
Tel: 0086-185-6889-5678
Factory: No.81 Donghui Second Street, Huangpu District, Guangzhou
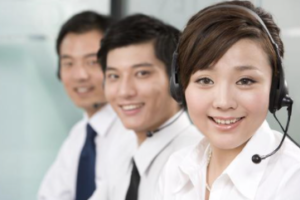