FAQ
Resistance welding is a welding method in which the workpiece to be welded is pressed between two electrodes, and the current is used to generate heat on the contact surface of the workpiece and the resistance in the adjacent area, and heat it to a molten or plastic state to form a metal bond. . With its unique advantages, resistance welding is widely used in aerospace, electronics, automobiles, household appliances and other manufacturing industries. There are four main resistance welding methods: spot welding, seam welding, projection welding, and butt welding.
Resistance welding is suitable for mass production, with high production efficiency and no noise and harmful gases; simple operation, easy to realize mechanization and automation; low welding cost, no welding materials such as filler metal; small stress and deformation, short heating time, and concentrated heat; The metallurgical process is simple. When the nugget is formed, it is always surrounded by a plastic ring, and the molten metal is isolated from the air.
The core of resistance welding are the three major elements of welding current, pressure, and energizing time, all of which are indispensable. Model selection according to the material and thickness of the workpiece.
Welding current is an important factor in generating heat. The formula is Q=I²Rt. It can be seen that the influence of current on heat generation is greater than both the resistance R and the time t. Therefore, the proper and stable welding current must be ensured during welding. If the welding current is too small, the welding part will not have enough heat, which will seriously affect the welding strength. If the welding current is too large, the welding part will be deformed, the surface will become dirty, the molten metal will splash, and bubbles will be generated.
Classification and Application of Resistance Welding
Principle and Application of Spot Welding Machine
Factors Affecting the Resistance Between Electrodes
Premium Product
Catalogue
News & Technicals
Structure of Nut Electrode of Intermediate Frequency Spot Welder
Analyze the Electrode of the Intermediate Frequency Spot Welder
Analyze the Influence of the Welding Point Distance of the Spot Welder
Function of Butt Welding Machine Inspection System
Contact Us
Email: info@resistancewelder.com
Tel: 0086-185-6889-5678
Factory: No.81 Donghui Second Street, Huangpu District, Guangzhou
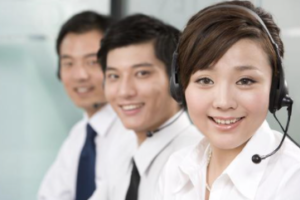