News & Technicals
Basic Knowledge of Resistance Welding
When using metal materials to make parts, it is often necessary to cut the material to a specified size and then connect them.
The methods of connecting materials include mechanical connection using rivets, metallurgical connection using welding, and physical connection using ultrasonic waves. Resistance spot welding is a method that uses metallurgy to connect metal materials efficiently and economically. Therefore, it is widely used in the industry.
We call resistance welding of precision small workpieces precision resistance spot welding.
Amada welding technology has continuously developed a variety of ultra-small, high-density installation of new precision resistance spot welding machines, replacing the previous metal connection processes such as soldering and riveting.
The precision resistance spot welding machine is most suitable for the assembly of small, high-performance electronic parts and small parts in the precision machinery industry.
Principles of resistance welding
Welding using Joule heat
Q=0.24I2Rt=0.24IEt(cal)…①
Formula ① As shown in the figure below, the workpiece is pressurized between the upper and lower electrodes, energized, and resistance welding is performed.
When the resistance of the welding part is R (Ω), the welding current is I (A), and the energization time is t (sec), the welding part generates heat according to the formula ①. Therefore, the temperature of the welded portion rises and melting occurs.
5 Major Elements of Resistance Spot Welding
1. Current
2. Time
3. Add pressure
4. Current density (the diameter of the electrode tip)
5. Electrode material
The above-mentioned elements are related to the heating value Q and the heating position, that is to say, the factors that affect the welding effect during spot welding are: current I, energization time t, contact resistance R, current density (electrode tip) and electrode material. The contact resistance R decreases with increasing pressure. The above elements are called the five elements of resistance spot welding.
Contact resistance
The resistance caused by the thin oxide layer formed on the surface of the workpiece (skin resistance) and the resistance caused by the cross section of the current flow (concentrated resistance)
The Usage of Electrodes
1. Conduct a large current.
2. put pressure on.
3. Improve the cooling effect of the solder joints.
4. Stable current density.
Electrodes have the above functions, here is an explanation of the current density related to quality management.
Current density refers to the current value per unit cross section. If the current density is kept constant, poor welding can be prevented. Due to the need to conduct a large current (electrode function 1), the tip of the electrode will heat up; and the pressure will make the tip of the electrode wider and the current density will decrease. Therefore, as the number of welding increases, the weld nugget will become smaller (welding Defects) Therefore, electrode management (replacement or grinding of electrodes after a certain number of welds) has become very important in welding quality management.
Send Message
Premium Product
Catalogue
News & Technicals
Structure of Nut Electrode of Intermediate Frequency Spot Welder
Analyze the Electrode of the Intermediate Frequency Spot Welder
Analyze the Influence of the Welding Point Distance of the Spot Welder
Function of Butt Welding Machine Inspection System
Contact Us
Email: info@resistancewelder.com
Tel: 0086-185-6889-5678
Factory: No.81 Donghui Second Street, Huangpu District, Guangzhou
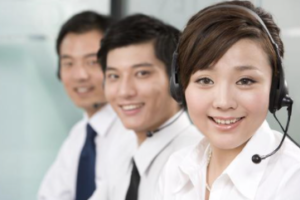