News & Technicals
Classification and Application of Resistance Welding
Types of Resistance Welding
Resistance welding refers to a method in which the resistance heat generated by the current passing through the weldment and the contact is used as a heat source to locally heat the weldment to a molten or plastic state, and at the same time press to form a metal bond. When welding, no filler metal is required, the productivity is high, the deformation of the weldment is small, and it is easy to realize automation.
According to the type of power source, there are three types: AC power resistance welding, secondary rectification resistance welding, and pulse power resistance welding.
Classified by process method, there are resistance spot welding, seam welding, projection welding, and resistance butt welding.
1. Spot welding is a resistance welding method in which the weldment is assembled into a lap joint and pressed between two electrodes to melt solid metal by resistance heat to form a welding spot. During spot welding, the weldment is only welded on a small contact area, forming a flat spherical nugget. Spot welding can be divided into single spot welding and multiple spot welding. In multi-spot welding, more than two groups of electrodes are required, and multiple nuggets are formed in the same process.
2. Seam welding is a resistance welding method in which the weldment is assembled into lap or butt joints and placed between two roller electrodes. The roller presses the weldment and rotates to continuously or intermittently supply electricity to form a continuous weld. During seam welding, after the weldment passes between the two roller electrodes, a continuous welding seam formed by lapped front and back of many welding points is formed. Seam welding is similar to spot welding, in essence, many welding points are regularly overlapped.
3. Projection welding is a variant of spot welding. It is a resistance welding method in which one or more raised points are pre-processed on the bonding surface of a weldment, so that it is in contact with the surface of another common part and is energized and heated, and then collapsed to make these contact points form solder joints. . One or more nuggets can be formed at the joint during projection welding.
4. Butt welding is a method of assembling the weldment into a butt joint so that its end faces are in close contact, using resistance heat to heat it to a plastic state, and then quickly applying upsetting force to complete the welding. During butt welding, the end faces of the two weldments are in contact, and the entire contact surface is welded through resistance heating and pressure. It can be divided into two forms: resistance butt welding and flash butt welding
Application and Usage of Resistance Welding
1: The production of various butt joints or ring parts with the same or similar cross-sections, such as the connection of construction steel bars and railway rails, the butt joint of dissimilar steel blanks for cutting tools, and the production of bicycles, motorcycles, and automobile rims.
2: Production of various thin plate or section steel parts, such as aircraft and automobile shell assembly, there are several million solder joints on the new passenger aircraft.
3: Assembling welding between various stamping parts and extruded parts and with thin plates.
4: Welding of spacecraft, semiconductor devices and integrated circuit components.
Premium Product
Catalogue
News & Technicals
Structure of Nut Electrode of Intermediate Frequency Spot Welder
Analyze the Electrode of the Intermediate Frequency Spot Welder
Analyze the Influence of the Welding Point Distance of the Spot Welder
Function of Butt Welding Machine Inspection System
Contact Us
Email: info@resistancewelder.com
Tel: 0086-185-6889-5678
Factory: No.81 Donghui Second Street, Huangpu District, Guangzhou
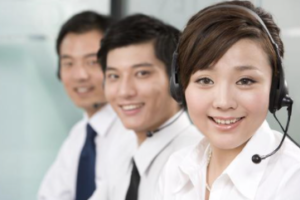