News & Technicals
Introduction of Spot Welding Process of Aluminum Plate
Classification and application of aluminum plates that can be resistance welded
According to the different metal element content of the material, aluminum plates in my country are classified into 1-9 series. Aluminum alloy parts that can be used in automobile manufacturing, such as automobile engine parts, steering parts, and surface coverings of high-end automobiles, and hardware appliances such as equipment and instrument housings, and supporting structures for electronic devices, such as TV section back panels, etc. ;
Because aluminum has high electrical conductivity and thermal conductivity, it is difficult to use resistance spot welding. Generally, the thickness of resistance spot welding used in civil and industrial products is generally less than 3+3mm, but there will be thicker aluminum in military or special industries. The material uses resistance welding spot welding technology.
Classification and characteristics of aluminum plate spot welding machine;
Resistance welding equipment that can be used for spot welding of aluminum plates mainly includes power frequency AC spot welders, medium frequency inverter DC spot welders, and capacitor energy storage welders.
Since the welding current of the power frequency AC welding machine is a 50HZ sine wave, there is a zero crossing point in a cycle, that is, the welding heat is not concentrated, and it is difficult to produce nuggets when welding aluminum plates. Therefore, it is currently used less in welding aluminum plates; The intermediate frequency inverter DC welding machine for aluminum plate is the most widely used. Because the welding current and welding time are convenient and adjustable, its welding current is stable, the heat is concentrated, and it is easy to adjust and control when welding aluminum materials. Therefore, it is the most widely used in the current aluminum plate welding. . With the continuous improvement of the current domestic production technology, intermediate frequency inverter equipment has also changed from relying on imports to exporting abroad.
The thermal efficiency of capacitor energy storage equipment is the most concentrated among the three types of welding equipment, but because the welding discharge time is not adjustable, it is easy to produce splashes when welding aluminum plates, and the electrode and the oxide layer are stuck. Therefore, there are not many aluminum materials welded with energy storage welding equipment.
Preparation and welding process before spot welding of aluminum plate
Aluminum is easily oxidized in contact with air, forming a dense oxide film AL2O3, which has poor electrical conductivity. If the oxide layer is thick and is not treated before welding, it is often difficult to produce nuggets during welding, the welding electrode is severely stuck, and cracks or shrinkage holes occur at the welding point. Therefore, the surface oxide layer should be treated before welding the aluminum plate without protective film. At present, the main treatment methods are: chemical treatment-pickling or alkaline cleaning; physical method-sandblasting, shot blasting, polishing, and gauze or wire brush.
In a complete welding process of the aluminum plate: first, the electrode needs to be brought into contact with the workpiece to be welded and pressure is applied; then it is energized, because there is resistance between the two overlapping materials of the workpiece when the current flows from the upper electrode through the workpiece to be welded to the lower electrode The value will generate resistance heat, the contact point will reach the molten state, and the mutual melting state will be formed under the action of the pressure of the upper and lower electrode heads to form a nugget, realizing the connection of the two contact surfaces
Inspection after resistance spot welding of aluminum plate
There are several methods for judging whether the welded product is qualified after resistance spot welding of aluminum plate: visual inspection, destruction experiment, ultrasonic X-ray inspection, and metallographic experiment of slicing.
Visual inspection: Observe by visual observation that the surface of the workpiece is too large, the gap in the welding overlap is too large, whether there are splash burrs, and whether there are cracks at the welding point, etc.
Destruction experiment: take the method of testing the test piece more-take the material with the same thickness and material as the workpiece to weld, and do the shearing, stretching or peeling experiment after the welding is completed, and use the detection performance of the test piece to judge whether the workpiece can reach Required performance requirements.
Ultrasonic X-ray inspection: In order to determine whether the product has a nugget and whether there are shrinkage holes and cracks in the nugget without damaging the product, it can be detected by ultrasonic and X-ray, and the digital signal is converted into graphic information, which can be accurate Image to determine the size of the weld nugget and the welding effect
Send Message
Premium Product
Catalogue
News & Technicals
Structure of Nut Electrode of Intermediate Frequency Spot Welder
Analyze the Electrode of the Intermediate Frequency Spot Welder
Analyze the Influence of the Welding Point Distance of the Spot Welder
Function of Butt Welding Machine Inspection System
Contact Us
Email: info@resistancewelder.com
Tel: 0086-185-6889-5678
Factory: No.81 Donghui Second Street, Huangpu District, Guangzhou
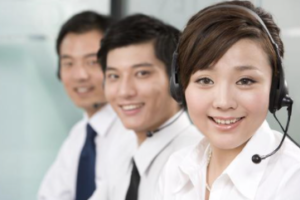