News & Technicals
Prevention Nut Missing for Nut Projection Welding Machine
The nut projection welding machine is a routine process in the automobile manufacturing industry. In addition to the strength, appearance, and position of the nut projection welding, this process also has a more difficult problem: the nut is missing sometimes.
Conventional solutions include installation of dot counters, full inspection of gages, automatic nut conveying projection welding, etc. The first type is low in cost, but requires manual resetting, and it is easy to cheat and cause missed welding; the second type is very reliable, However, it requires an additional station and manual full inspection, and the production cost is high. Although the reliability and efficiency of the third type are higher, the one-time investment is relatively large, and the type change is inconvenient, and it is not suitable for small batch switching.
Instruction of Prevent Nut Missing
It is composed of photoelectric sensor switch, PLC, touch screen, positioning fixture and photoelectric door;
Working Principle:
1. Confirm the uniqueness of the projection welding position of the head and tail nut. The position of the first and last projection welding nut on each set of welding parts is fixed. It is realized by the nut electrode, cylinder floating positioning stopper or positioning pin, and a photoelectric sensor switch is used to sense and control this position. confirm;
2. The projection welding position and sequence control of the head and tail nut. The projection welding sequence of the first and last nut is determined by PLC. Only when the parts and nuts are placed in the set position and sequence and the welding is started will it be effective; the welding sequence of the middle part nut is not required and does not detect the position but must be welded The quantity meets the requirements.
3. Confirm whether there is a projection welding nut. After starting welding, the cylinder will be tested for the presence or absence of projection weld nuts before pressing down and energizing welding. This detection switch is installed on the upper electrode platform. When there is a welding nut, the electrode position is higher, and the sensing block is aligned with the sensing switch. The sensing switch considers that the nut is detected and allows energized welding. Otherwise, it will not be energized and give an alarm.
4. Confirm the number of projection welding nuts. Each time a nut is welded, the welding controller will give a welding end model to the counter, and the counter will output a permit signal when the set number of nuts is reached;
5. Confirm the end of the welding cycle. When all the nuts on a piece are welded and the count is correct, manually put the parts into the material box through the photoelectric gate, and the photoelectric gate senses the putting action, that is, confirms that a correct and complete welding cycle is completed, and allows the next welding cycle.
Send Message
Premium Product
Catalogue
News & Technicals
Structure of Nut Electrode of Intermediate Frequency Spot Welder
Analyze the Electrode of the Intermediate Frequency Spot Welder
Analyze the Influence of the Welding Point Distance of the Spot Welder
Function of Butt Welding Machine Inspection System
Contact Us
Email: info@resistancewelder.com
Tel: 0086-185-6889-5678
Factory: No.81 Donghui Second Street, Huangpu District, Guangzhou
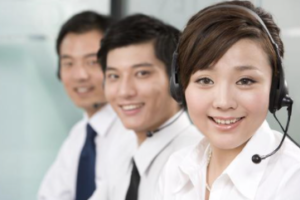