News & Technicals
Principle and Application of Spot Welding Machine
Spot welding is where the weldment is welded at individual points on the contact surface at the joint. Spot welding requires the metal to have better plasticity. When welding, clean the surface of the weldment first, and then lap the welded sheet to be assembled, press it between the two columnar copper electrodes, and apply force to compress it. When a large enough current is passed, a large amount of resistance heat is generated at the contact of the plates, and the metal in the hottest area in the center is quickly heated to a high plasticity or molten state, forming a lens-shaped liquid molten pool. Continue to maintain the pressure, disconnect the current, and after the metal cools, a solder joint is formed.
Spot welding is only used for the welding of thin-plate lap joints, metal meshes, and cross-reinforced structural parts that do not require tightness due to the certain distance between the welding points. If the cylindrical electrode is replaced with a disc-shaped electrode, the electrode presses the weldment tightly and rotates, and the weldment is continuously fed in between the disc-shaped electrode, and then is energized with pulse. A continuous and overlapping welding spot can be formed to form a weld, which is seam welding. It is mainly used for welding thin-plate overlapping structural parts with sealing requirements or higher joint strength requirements, such as fuel tanks, water tanks, etc.
Welding machines are classified according to their purposes, including universal (universal) and special-purpose types. According to the number of solder joints welded at the same time, there are single-point, double-point, and multi-point types. According to the transmission mode of the pressurizing mechanism, there are pedal type, motor-cam type, pneumatic type, hydraulic type, compound type (pneumatic and hydraulic combined type) and so on.
Premium Product
Catalogue
News & Technicals
Structure of Nut Electrode of Intermediate Frequency Spot Welder
Analyze the Electrode of the Intermediate Frequency Spot Welder
Analyze the Influence of the Welding Point Distance of the Spot Welder
Function of Butt Welding Machine Inspection System
Contact Us
Email: info@resistancewelder.com
Tel: 0086-185-6889-5678
Factory: No.81 Donghui Second Street, Huangpu District, Guangzhou
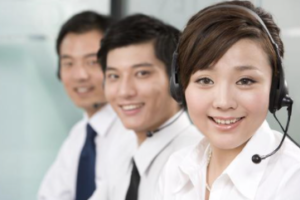