News & Technicals
Welding Methods of Electric Resistance Welding Machine
1. Spot Welding
Spot welding is a resistance welding method in which the weldment is equipped with a lap joint and pressed between two cylindrical electrodes to deceive the resistance to heat the base metal to cause the welding spot. Spot welding is mainly used for thin plate welding.
The process of spot welding:
(1) Pre-compression to ensure good contact of the workpiece.
(2) Energize to cause nugget and plastic ring at the weld.
(3) Power-off forging, so that the nugget will cool and crystallize under the continuous action of pressure, resulting in a solder joint with dense structure, no shrinkage, and cracks.
2. Seam Welding
The process of seam welding is similar to spot welding, except that the rotating disc-shaped roller electrode replaces the cylindrical electrode, and the weldment is equipped with lap or butt joints and placed between the two roller electrodes. The roller presses the weldment and Rotation, continuous or intermittent power supply, resulting in a continuous welding seam resistance welding method. Seam welding is mainly used for welding structures with more regular welds and requiring sealing. The thickness of the plate is usually below 3mm.
3. Butt Welding
Butt welding is a resistance welding method in which the weldment is welded along all contact surfaces.
(1) Resistance butt welding
Resistance butt welding is a method in which the weldment is equipped with butt joints so that the end faces are in close contact, and the resistance is heated to a plastic form, then the power is cut off and the upsetting force is quickly applied to complete the welding.
Resistance butt welding is mainly used for weldments with simple cross-section, diameter or side length less than 20mm, and low strength requirements.
(2) Flash butt welding
Flash butt welding is to equip the weldment as a butt joint, turn on the power, and make the end face gradually move closer to the one-sided contact, and the resistance heats these contact points. Under the action of large current, flash occurs and the end face metal is melted until the end is reached. When the part reaches the predetermined temperature within the certain depth boundary, the power is cut off and the upsetting force is quickly applied to complete the welding.
The quality of the joint of flash welding is better than that of resistance welding, the mechanical function of the weld is equal to that of the base metal, and there is no need to arrange the pre-welded surface of the joint before welding. Flash butt welding is often used for welding important weldments. It can weld the same kind of metal, and also can weld dissimilar metals; it can weld 0.01mm metal wire, and also can weld 20,000mm metal rod and profile.
4. Projection Welding
Projection welding is a modified mode of spot welding; there are prefabricated bumps on a workpiece, and during projection welding, one or more nuggets can be created at the joint at a time.
The quality of resistance welding is determined by the following 4 factors:
1. Current, 2. Time when energized, 3. Pressure, 4. Diameter of the resistor tip
Send Message
Premium Product
Catalogue
News & Technicals
Structure of Nut Electrode of Intermediate Frequency Spot Welder
Analyze the Electrode of the Intermediate Frequency Spot Welder
Analyze the Influence of the Welding Point Distance of the Spot Welder
Function of Butt Welding Machine Inspection System
Contact Us
Email: info@resistancewelder.com
Tel: 0086-185-6889-5678
Factory: No.81 Donghui Second Street, Huangpu District, Guangzhou
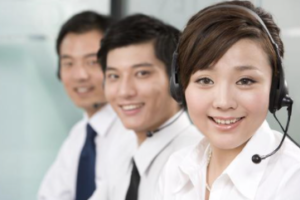